Researchers have developed a novel approach to analyze the internal structure of aluminum and its oxide coatings using neutron imaging. This technique provides insights into the hydrogen content, corrosion, and other properties that are crucial for industries relying on aluminum components. By combining advanced simulation models and filtering methods, the scientists were able to separate the effects of neutron refraction and attenuation, unlocking a deeper understanding of these materials. This breakthrough could pave the way for improved quality control and design optimization in applications ranging from aerospace to consumer electronics. Neutron imaging has emerged as a powerful tool for material characterization, and this research demonstrates its versatility in tackling complex challenges.
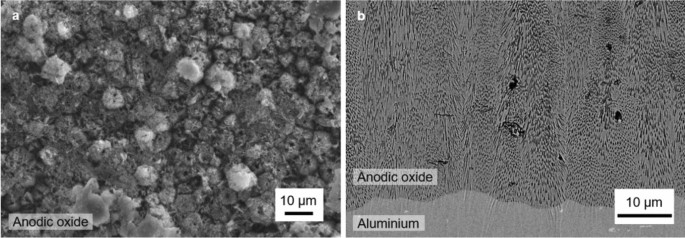
Unraveling the Mysteries of Aluminum
Aluminum is a ubiquitous material in modern society, found in everything from airplane fuselages to beverage cans. Its lightweight, corrosion-resistant, and conductive properties make it an essential component in a wide range of industries. However, understanding the intricate details of aluminum’s structure and behavior can be a challenge, especially when it comes to the delicate oxide layer that forms on its surface.
Neutrons Reveal the Hidden Layers
The research team, led by scientists from the Technical University of Denmark and the Paul Scherrer Institute in Switzerland, turned to neutron imaging to shed light on the internal structure of aluminum and its oxide coatings. Neutrons, unlike X-rays, are highly sensitive to the presence of hydrogen and can penetrate deep into metallic materials, making them a powerful tool for visualizing the distribution of elements within a sample.
Separating Signals: Phase and Attenuation
The researchers faced a challenge, however, as the neutron beam can be refracted, or bent, when it encounters the interfaces between different materials. This “phase effect” can distort the attenuation signal, which is the measure of how much the neutrons are absorbed or scattered by the sample. To overcome this, the team explored two approaches: a traditional phase filtering method and a novel simulation-based technique.
The phase filtering method, adapted from X-ray imaging, was able to remove the phase effects for the simple aluminum sample. However, for the more complex oxide-coated aluminum, the filtering introduced significant blurring, obscuring important details about the material’s structure.
Simulating the Way Forward
The researchers then turned to a simulation-based approach, using the McStas ray-tracing software to model the neutron interactions with the samples. By iteratively adjusting the simulation parameters to match the experimental data, the team was able to generate a “pure” attenuation signal, effectively separating the phase and attenuation effects.
This simulation-based approach proved superior to the phase filtering method, allowing the researchers to uncover subtle variations in the oxide layer’s composition and structure that were previously obscured. The insights gained from this work could lead to improved quality control and design optimization for aluminum-based products, benefiting industries ranging from aerospace to consumer electronics.
A Promising Path for the Future
The success of the simulation-based approach suggests that it could be a valuable tool for other complex materials and imaging challenges. By combining advanced simulation models with experimental data, researchers can gain a deeper understanding of the underlying material properties and overcome the limitations of traditional analysis methods.
As the field of neutron imaging continues to evolve, this research highlights the importance of interdisciplinary collaboration and the integration of simulation and experimental techniques. By harnessing the unique capabilities of neutrons, scientists can unlock new insights into the materials that shape our world, paving the way for innovative solutions to complex challenges.
Author credit: This article is based on research by Estrid Buhl Naver, Okan Yetik, Noémie Ott, Matteo Busi, Pavel Trtik, Luise Theil Kuhn, Markus Strobl.
For More Related Articles Click Here