Researchers have developed a novel brush-plated nickel coating infused with polytetrafluoroethylene (PTFE) particles, resulting in a hydrophobic and low-friction surface that offers enhanced protection against corrosion. This innovative coating combines the strength of nickel with the non-stick properties of PTFE, creating a versatile material with potential applications in harsh environments. The study provides insights into the unique growth mechanism and impressive performance characteristics of this advanced composite coating. Nickel, PTFE, and their combination open up exciting possibilities for improving the durability and functionality of various engineered surfaces.
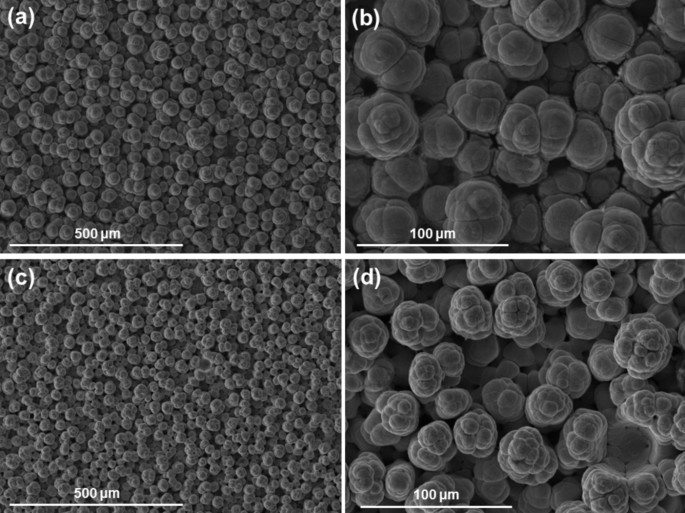
Combining the Strength of Nickel and the Slipperiness of PTFE
In the pursuit of robust and versatile coatings, researchers have explored the synergistic potential of combining nickel and polytetrafluoroethylene (PTFE). Nickel is a popular choice for its impressive strength, corrosion resistance, and ease of electroplating, while PTFE, commonly known as Teflon, is revered for its exceptional non-stick and hydrophobic properties.
The researchers in this study have developed a novel brush-plated coating that integrates the best of both materials, creating a unique Ni/PTFE composite with enhanced performance characteristics. The key innovation lies in the coating’s unique growth mechanism, which results in a bilayer-like structure with a smooth, compact PTFE top layer covering a rougher nickel sublayer.
Overcoming the Challenges of PTFE Suspension
One of the primary challenges in producing Ni/PTFE composite coatings is the inherent hydrophobicity of PTFE particles, which makes them difficult to suspend in aqueous plating solutions. The researchers explored various approaches to address this, including the use of cationic surfactants and alcohols as suspending agents.
While the cationic surfactant CTAB successfully suspended the PTFE particles, it failed to enable the co-deposition of PTFE onto the nickel coating. In contrast, the use of isopropyl alcohol (IPA) and ethanol proved more successful, allowing the PTFE particles to be incorporated into the nickel matrix during the brush-plating process.
The Formation of a Unique Bilayer Structure
The researchers observed that the Ni/PTFE coatings produced with IPA and ethanol exhibited a distinctive bilayer-like structure. Initially, a rough nickel sublayer is deposited, which then serves as a substrate for the PTFE particles to bind and grow, forming a smooth, compact top layer.
This unique growth mechanism is believed to be driven by the localized heating generated by the electric current passing through the non-conductive PTFE particles. The heat helps to fuse the PTFE particles together, creating the continuous outer layer without the need for a separate baking stage.
Impressive Performance Characteristics
The resulting Ni/PTFE coatings demonstrate several impressive performance characteristics. The hydrophobic PTFE top layer provides a water contact angle of around 109 degrees, approaching the values of pure PTFE. This hydrophobicity, combined with the smooth surface, is expected to enhance the coatings’ resistance to corrosion in harsh environments.
Furthermore, the Ni/PTFE coatings exhibit a significantly lower coefficient of friction compared to pure nickel coatings, with values around 0.10. This low friction can be attributed to the slippery nature of the PTFE top layer, making the coatings well-suited for applications where wear and sliding resistance are crucial.
Potential Applications and Future Developments
The Ni/PTFE composite coatings developed in this study hold promise for a wide range of applications, particularly in environments where corrosion, friction, and wear are major concerns. These coatings could find use in industries such as automotive, aerospace, and marine engineering, where their unique properties can help extend the lifespan and functionality of critical components.
As the research continues, further optimization of the coating process and exploration of alternative suspension agents may lead to even more advanced Ni/PTFE composites with enhanced performance characteristics. The versatility of this approach also opens up possibilities for incorporating other functional materials, such as ceramics or carbon nanotubes, into the nickel matrix to create tailored coatings for specific applications.
Author credit: This article is based on research by L. Isern, S. Impey, H. Almond, S. J. Clouser, J. L. Endrino.
For More Related Articles Click Here