Discover how innovative materials science is paving the way for the next generation of gas turbines, capable of operating on clean hydrogen fuel and reaching unprecedented temperatures. This breakthrough technology holds the promise of a more sustainable energy future. Gas turbines and power generation are set to undergo a transformative shift.
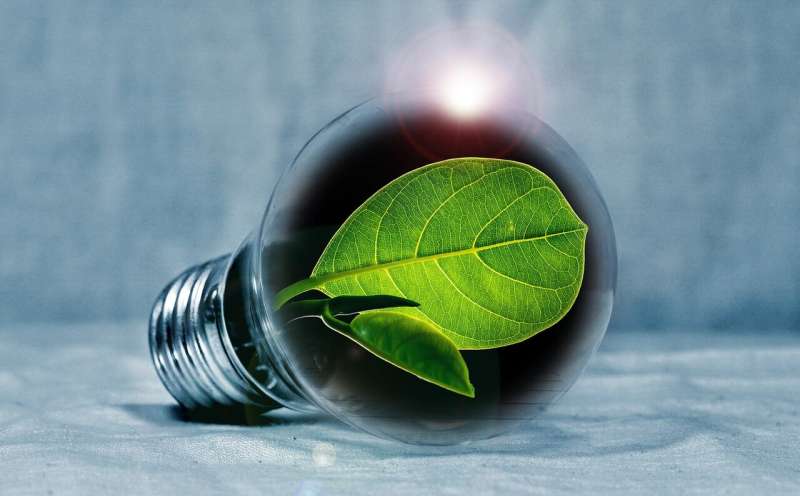
Jose Ruiz on New Epoch of Hydrogen Turbines
Marine engineer Charles Parsons’ invention of the multi-stage steam turbine in 1884 paved a path to great quantities of cheap energy by changing how we generate and consume power. Skip forward to the present, and an increasingly energy-hungry globe requires more efficient, cleaner turbine technologies.
At Texas A&M, engineers are working on a materials system that can operate gas turbines with hydrogen fuel rather than natural gas. Part of a larger scheme by the US to eliminate emissions in its energy sector by 2035, it is an ambitious goal. By switching from natural gas to hydrogen, these new turbines could cut carbon dioxide emissions dramatically — and provide enough power when the world needs it most.
Addressing the Difficulties of High-temperature Hydrogen Combustion
Hydrogen-powered turbines have unique challenges of their own to address, as they break with traditional combustion processes. Turbines require that they are heated a great deal, anywhere from 3000°F and upwards, in order to be at their most efficient. Even nickel-based superalloys used in traditional turbine blades begin to melt at 2400°F, which just isn’t up to the challenge for something converting immense forces into power.
The researchers are looking into a new class of materials called refractory high entropy alloys (RHEAs), many with melting temperatures greater than 3500°F, to overcome this challenge and have used advanced alloy design tools to identify RHEA candidates that are suited for use as structural materials in a hydrogen-fired gas turbine subject to the extreme heat and pressures. However, that is not all — these materials must also be oxidation-resistant and capable of withstanding the high moisture environment caused by burning hydrogen.
Hydrogen-Turbine Simulation In Violent Conditions
In an experiment designed to closely mimic the environment at the hottest part of a hydrogen-fired gas turbine, where materials must withstand both high temperatures and extreme vibration, the researchers have tested how resilient their system is when it comes to RHEA materials. Under high pressures hydrogen and air is forced through small rocket-nozzle shaped tubes, where it is ignited producing high temperature, velocity gas and steam wich leaves the nozzle at supersonic speeds to imping on the RHEA coupons.
The testing, which involves performance evaluation of the alloy substrate, oxidation-resistant coating and thermal barrier coating is expected to deliver results on whether RHEAs are a viable option for hydrogen gas turbines. With this knowledge of how these materials will react under real hydrogen conditions, the designers can then create new improved designs and work towards unlocking the full potential of the technology.