
Ensuring the optimal performance and longevity of wind turbines is crucial for the clean energy industry. In a groundbreaking study, a team of researchers has developed a highly accurate and lightweight algorithm that can automatically detect a wide range of surface defects in wind turbines, paving the way for more efficient maintenance and improved reliability of these vital renewable energy sources. The algorithm, based on the popular YOLO object detection framework, leverages innovative techniques like convolutional neural networks and attention mechanisms to precisely identify cracks, erosion, leaks, dirt, and paint damage on wind turbine surfaces. This groundbreaking work could revolutionize the wind energy industry, leading to significant cost savings and reduced environmental impact.
Empowering Wind Turbine Maintenance with Advanced Defect Detection
Maintaining the structural integrity and optimal performance of wind turbines is a critical challenge in the renewable energy sector. These towering structures endure constant stress from wind, weather, and mechanical forces, leading to a variety of surface defects that can compromise their efficiency and lifespan. Traditionally, inspecting and repairing these defects has been a time-consuming and labor-intensive process, often requiring manual inspections by skilled technicians.
To address this challenge, a team of researchers from Beihua University in China has developed a cutting-edge algorithm that can automatically detect a wide range of surface defects in wind turbines. The algorithm, based on the popular YOLO (You Only Look Once) object detection framework, utilizes a combination of innovative techniques to achieve high accuracy and a lightweight design suitable for deployment on resource-constrained edge devices.
Unlocking the Power of Multiscale Feature Extraction
At the core of the algorithm is the PC-EMA (Partial Convolution and Efficient Multiscale Attention) module, which enhances the feature extraction capabilities of the backbone network. This module employs partial convolution to efficiently extract spatial features, while the efficient multiscale attention mechanism ensures that the network can effectively capture and process features at different scales. This approach is particularly crucial for detecting small or subtle defects, which can be easily overlooked by traditional methods.
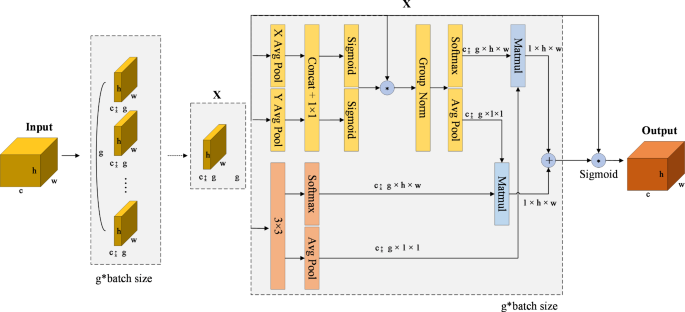
Optimizing for Lightweight and Real-Time Performance
To ensure the algorithm’s suitability for real-world deployment, the researchers have also made significant improvements to the network’s neck and head sections. They introduced the GSConv (Grouped Shuffle Convolution) and VoVGSCSP modules, which reduce the computational complexity of the feature fusion process without compromising the model’s accuracy. Additionally, the team designed a PConv Head, which merges the classification and regression tasks into a single, efficient convolutional layer, dramatically reducing the number of parameters and improving the model’s inference speed.
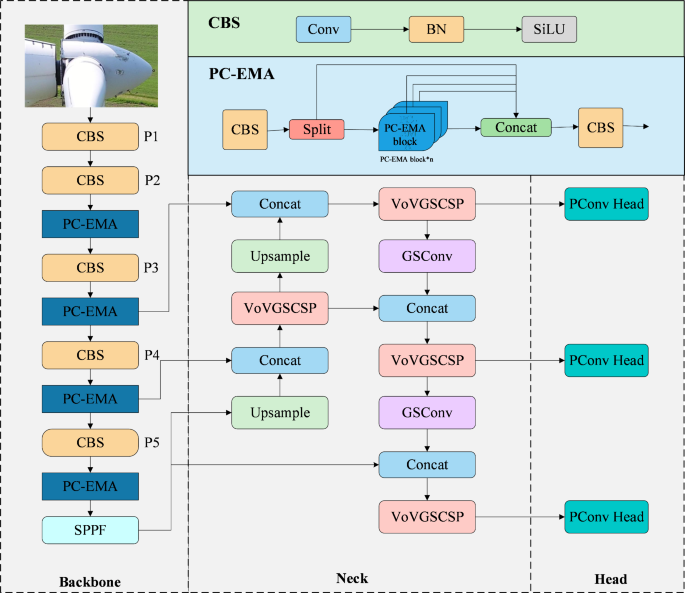
Fig. 2
Enhancing Defect Detection Accuracy with Wise IoU
To further boost the accuracy of the defect detection, the researchers introduced the WIoUv3 (Wise Intersection over Union) loss function. This novel loss function takes into account the size differences between the target bounding boxes, ensuring that the model pays more attention to the common quality samples and improving its overall localization capabilities.
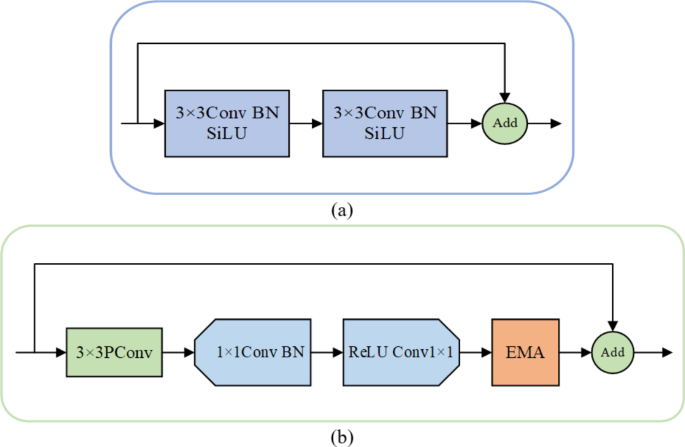
Fig. 3
Versatile and Robust Performance
The researchers’ comprehensive evaluation of the algorithm on a custom wind turbine defect dataset, as well as its deployment on the resource-constrained Jetson Nano platform, demonstrates its exceptional performance. Compared to other state-of-the-art object detection models, the algorithm achieves a higher mean average precision (mAP) of 5.07% while being 32.5% smaller in size and 11 frames per second (FPS) faster on the Jetson Nano.
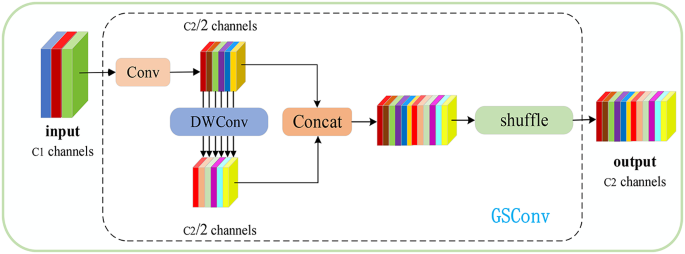
Fig. 4
Revolutionizing Wind Turbine Maintenance and Beyond
The development of this highly accurate and lightweight defect detection algorithm represents a significant breakthrough in the field of wind turbine maintenance and monitoring. By automating the inspection process and enabling real-time, on-site detection of a wide range of surface defects, the algorithm has the potential to revolutionize the way wind turbines are maintained, leading to substantial cost savings, improved reliability, and reduced environmental impact.
Furthermore, the versatility of the algorithm suggests that it could be adapted and applied to a wide range of industrial inspection and monitoring tasks, beyond just wind turbines. The team’s innovative approach to feature extraction, model optimization, and loss function design could inspire future advancements in the field of computer vision and deep learning for industrial applications.
Author credit: This article is based on research by Zhenjie Wu, Yulu Zhang, Xiang Wang, Haofei Li, Yuyang Sun, Gang Wang.
For More Related Articles Click Here