Plastic pollution is a global crisis, with millions of tons of plastic waste ending up in landfills and oceans every year. However, researchers have discovered a remarkable solution that not only addresses this environmental challenge but also enhances the performance and durability of road pavements. A team of scientists from the Indian Institute of Technology (BHU) Varanasi has successfully incorporated low-density polyethylene (LDPE) – a common plastic waste material – into asphalt concrete (AC) mixtures, creating a sustainable and high-performance paving solution. This innovative approach not only repurposes plastic waste but also outperforms conventional asphalt mixes in key areas like stiffness, resistance to deformation, and fatigue life. Plastic pollution is a global crisis, and this research offers a promising pathway to tackle this issue while revolutionizing the construction of roads and highways.
Tackling the Plastic Waste Crisis through Sustainable Road Construction
The global production and use of plastics have been steadily increasing, outpacing recycling efforts. In India alone, plastic waste constitutes around 10% of the municipal solid waste, with low-density polyethylene (LDPE) being the most prevalent type. Despite efforts to manage this waste, only about 50% is properly disposed of and recycled, leading to significant environmental degradation. Traditional disposal methods like landfilling and incineration are found to be inadequate due to limited land availability, pollution, and high costs.
Transforming Plastic Waste into High-Performance Asphalt Mixtures
Recognizing the urgent need for effective waste management strategies, researchers at the Indian Institute of Technology (BHU) Varanasi have developed a groundbreaking solution. They have successfully incorporated LDPE plastic waste into asphalt concrete (AC) mixtures, creating a sustainable and high-performance paving material.
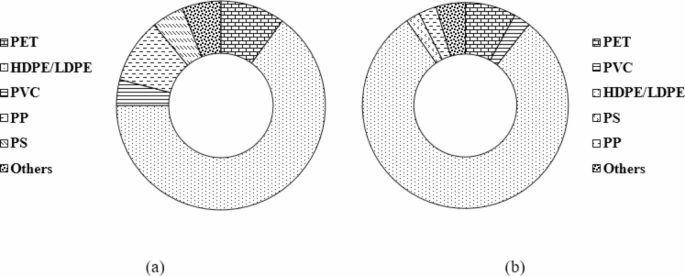
The researchers modified the conventional asphalt binder by blending it with LDPE pellets, creating a LDPE-modified asphalt binder. This modified binder was then used to prepare AC mixtures and compared with those made using commonly used binders, such as VG 30, VG 40, Polymer-Modified Binder (PMB), and Crumb Rubber Modified Binder (CRMB).
Exceptional Mechanical Performance
The results of the study were remarkable. The LDPE-modified AC mixtures exhibited superior mechanical performance compared to the conventional mixes:
– Stiffness: The LDPE-modified mixtures showed a 171% and 125% increase in stiffness (resilient modulus) at 25°C and 35°C, respectively, compared to the VG 30 base binder.
– Tensile Strength: The indirect tensile strength (ITS) of the LDPE-modified mixtures improved by 51% over the VG 30 binder.
– Resistance to Permanent Deformation: The LDPE-modified mixtures showed up to 133.46% higher Rutting Tolerance Index (RTIndex) values than the VG 30 binder, indicating superior resistance to permanent deformation.
– Fatigue Resistance: The LDPE-modified mixtures exhibited higher fatigue resistance, as indicated by increased Cracking Tolerance Index (CTIndex) values compared to the VG 30 and CRMB mixes.
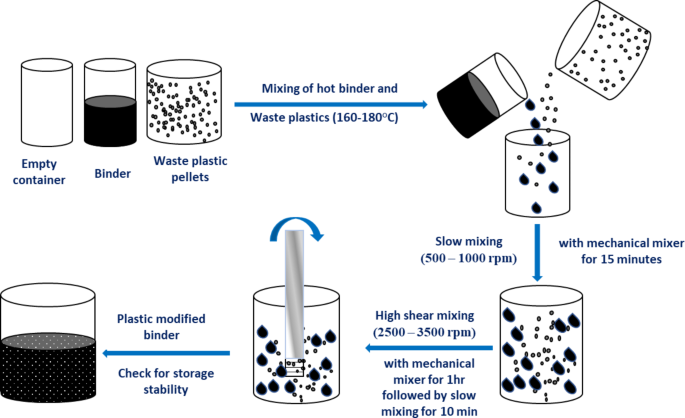
Table 1 Mechanical properties of the aggregates used.
These exceptional mechanical properties of the LDPE-modified AC mixtures can be attributed to the improved interaction between the LDPE and the asphalt binder, leading to enhanced stiffness, strength, and resistance to deformation and cracking.
Pavement Performance and Economic Feasibility
The researchers further evaluated the performance of the LDPE-modified pavements using advanced 3D-Move analysis software. The results were equally impressive:
– Reduced Pavement Deformation: The LDPE-modified pavements showed lesser deflections at the pavement layer interfaces, resulting in higher rutting and fatigue life compared to other pavements.
– Improved Fatigue and Rutting Life: The LDPE-modified pavements exhibited up to 57% higher fatigue life and up to 42.33% higher rutting life than other pavements.
In terms of economic feasibility, the cost of the LDPE-modified pavements was found to be comparable to the VG 40 binder and around 10% more economical than pavements containing the PMB binder. Additionally, the use of LDPE offers environmental benefits by repurposing up to 750 kg of plastic waste for every kilometer of single-lane pavement section with a 50mm thick surface course.
A Sustainable and Scalable Solution
The findings of this research study demonstrate the immense potential of LDPE-modified asphalt mixtures as a sustainable and high-performance solution for road construction. By integrating plastic waste into the pavement, this innovative approach not only addresses the global plastic pollution crisis but also enhances the durability and longevity of roads and highways.
Toward a Greener Future
As the world grapples with the pressing issue of plastic waste, the research conducted at the Indian Institute of Technology (BHU) Varanasi offers a promising pathway to transform this challenge into an opportunity. By repurposing LDPE plastic waste into high-performance asphalt mixtures, this groundbreaking solution paves the way for a more sustainable and environmentally friendly future in the construction of roads and infrastructure.
Author credit: This article is based on research by Aakash Singh, Ankit Gupta.
For More Related Articles Click Here