As plastic waste piles up faster than it can decompose, the search for eco-friendly solutions has never been more pressing. Researchers at Osaka Metropolitan University have developed a game-changing strategy to improve the production of fumaric acid, a critical raw material for biodegradable plastics. By adopting a “more haste, less speed” approach, they’ve significantly boosted the efficiency of the conversion process, opening new doors for a sustainable future. Fumaric acid and biodegradable plastics are at the forefront of this environmental revolution.
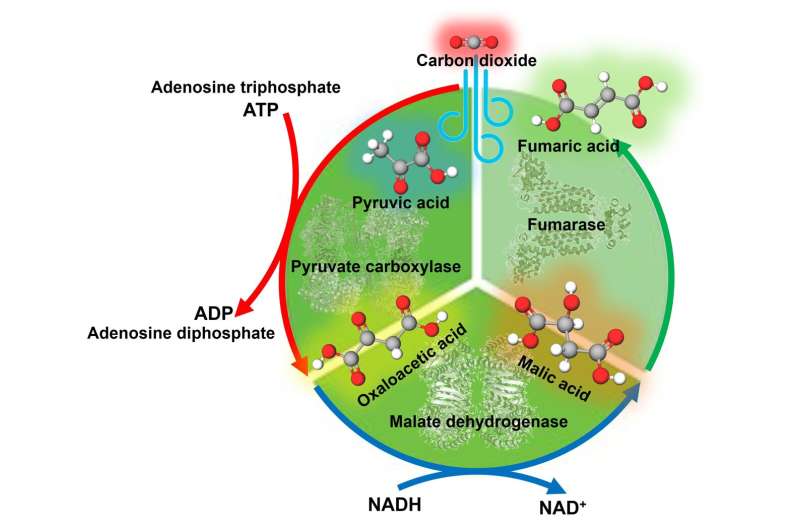
Converting Biomass And Co2
Under the leadership of Prof. Yutaka Amao, a research team has been successful at producing fumaric acid, an essential raw material for biodegradable plastics. Even beer has been squeezed from PS I before; their previous paper showed that they could make fumaric acid, using the reaction between pyruvic acid derived from biomass and carbon dioxide. But the process also suffered from by-production of alien chemicals and a necessary intermediary, L-malic acid.
Undaunted, the researchers came up with a “double negative” based plan that replaced one set of reactions performed by a single enzyme, malate dehydrogenase decarboxylase, with two different enzymes. Their work has certianly turned heads, and the team’s success is documented in a recently-published article published in the RSC journal, Sustainability.
Improved efficiency, more features
The team’s innovative new approach increased the efficiency of this process that creates fumaric acid. Through optimization of the reaction system, 80% of pyruvic acid could be converted into L-malic acid in 5 hours, a significant improvement over the previous work that only managed to convert 46% within 7 hours. Moreover, the further addition of fumarase to the reaction will enhance not only pyruvic acid, but also a remarkable 16% yield within five hours from 10%.
This discovery is profound in its implications. Professor Amao said, “In the conventional fumaric acid production system, only pure carbon dioxide gas could be used. This research has demonstrated that low-concentration carbon dioxide gas from thermal power plants and steel mills can be used.” The increased feedstock availability might largely improve the life cycle impact as well as scaling-up of fumaric acid production; and therefore might make it a more commercially viable solution for reducing use of nondegradable plastics.
Harnessing the Power of Light
For authors, this goes beyond perfecting the chemical process. They have also started working on a method of building chemical synthesis techniques in which the principles of artificial photosynthesis are simulated to produce fumaric acid using light energy. In the process, renewable solar energy could also be used to drive the conversion process, resulting in even greater sustainability of fumaric acid production.
The promise of this research is pretty compelling. With efficiency gains and more choices of feedstock to make fumaric acid, the work of the Osaka Metropolitan University team can bring us closer to a world which uses such acids in a more sustainable way. Therella too sets a bold example of what can be done through innovative and lateral thinking pathways in terms of unlocking the potential of bio-based materials, to make a circular economy transition; as demands escalate on moving towards biodegradable options.